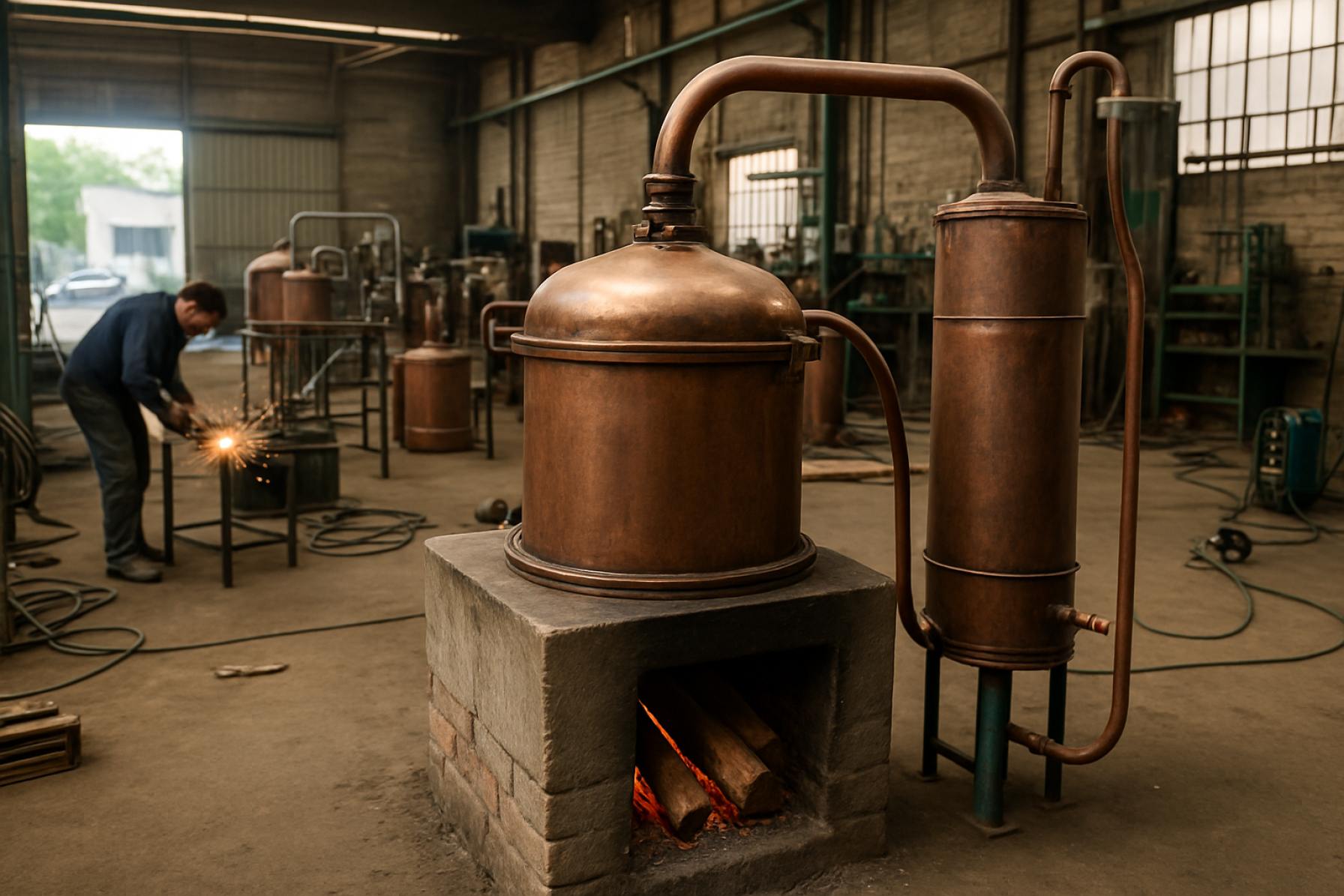
Table of Contents
- Executive Summary and Industry Overview
- Global Market Size, Trends, and Forecasts (2025–2030)
- Key Players and Competitive Landscape
- Raw Materials Sourcing and Regulatory Compliance
- Advancements in Distillation Technologies and Automation
- Sustainability: Eco-friendly Manufacturing and Waste Management
- Supply Chain and Distribution Channels
- Regional Analysis: Production Hotspots and Emerging Markets
- Customer Segments and End-User Applications
- Future Outlook: Challenges, Opportunities, and Strategic Recommendations
- Sources & References
Executive Summary and Industry Overview
The global sandalwood distillation apparatus manufacturing sector is poised for steady growth through 2025 and the next few years, driven by increasing demand for natural essential oils and a resurgence of interest in traditional extraction methods. Sandalwood oil, valued for its fragrance and therapeutic properties, necessitates specialized distillation equipment capable of handling the unique requirements of the wood’s dense, resinous character. Manufacturers are responding by innovating apparatus designs that improve yield, energy efficiency, and ease of operation.
Key industry players such as www.essencetech.com, shivaengineers.com, and www.shriramequipments.com are leading developments in both batch and continuous distillation systems. These companies are investing in stainless steel and hybrid material reactors, automated controls, and modular setups to meet the evolving needs of small-scale producers and larger commercial distillers alike. Notably, demand for turnkey plants—integrating wood chippers, steam distillation vessels, condensers, and oil-water separators—has risen, especially in regions such as India and Australia, which remain the primary sources of legal sandalwood cultivation and processing.
In 2025, the industry is witnessing a surge in orders from artisanal distillers and cooperative societies, reflecting a broader trend towards traceable, locally-produced sandalwood oil. Manufacturers are adapting to this shift by offering scalable apparatus and after-sales technical support, as highlighted by www.essencetech.com and shivaengineers.com. Furthermore, sustainability and regulatory compliance are shaping apparatus design, with a focus on minimizing water and energy consumption and ensuring emissions standards are met.
Looking ahead, the next few years are expected to see continued digitalization in apparatus control and monitoring, with remote diagnostics and IoT-based sensors becoming increasingly standard. Customization will remain a key differentiator, with companies like www.shriramequipments.com offering bespoke solutions for specific feedstock qualities and output requirements. Collaboration with research organizations and end-users is also fostering innovation, particularly in maximizing oil yield and reducing processing times.
In summary, the sandalwood distillation apparatus manufacturing sector in 2025 is marked by technological advancement, expanding end-user base, and a strong orientation toward efficiency and sustainability. Market outlook remains positive, underpinned by robust demand for sandalwood oil and ongoing modernization of extraction infrastructure.
Global Market Size, Trends, and Forecasts (2025–2030)
The global market for sandalwood distillation apparatus manufacturing is poised for steady growth between 2025 and 2030, reflecting rising demand for high-value essential oils and increasing investments in sustainable distillation technologies. Sandalwood oil remains a coveted commodity in perfumery, cosmetics, and traditional medicine, which has, in turn, catalyzed technological advancements and capacity expansion among apparatus manufacturers.
In 2025, the sandalwood distillation apparatus sector is characterized by a combination of traditional batch distillation units and modern, semi-automated systems, with manufacturers such as www.rameshmachines.com and www.sweedal.com leading innovation in India—one of the world’s major sandalwood processing hubs. These companies are increasingly offering stainless steel and copper distillation units in varied capacities, addressing both artisanal and industrial-scale needs.
Globally, Southeast Asia and Australia remain prominent markets for distillation equipment, driven by their established sandalwood plantations and export-oriented oil extraction operations. Australian manufacturers, such as www.essentialoilengineers.com.au, are focusing on energy-efficient designs and automation to meet sustainability criteria and regulatory requirements in international markets.
- Market Size & Growth: Industry estimates from direct manufacturer disclosures indicate that the global demand for sandalwood distillation systems is growing at a CAGR of 7–9% through 2030, with Asia-Pacific accounting for over 60% of new installations (www.sweedal.com).
- Technological Trends: Manufacturers are integrating improved heat exchangers, digital process controls, and modular designs to boost yield and reduce energy usage, as seen in recent product launches by www.rameshmachines.com.
- Sustainability Focus: There is a discernible shift towards closed-loop water systems and reduced waste emissions in apparatus design, in response to both environmental regulations and end-user demand for greener operations (www.essentialoilengineers.com.au).
- Regional Dynamics: Expansion of sandalwood cultivation in China and Southeast Asia is expected to further stimulate regional apparatus manufacturing and exports through 2030.
Looking ahead, the sandalwood distillation apparatus manufacturing industry is likely to witness continued consolidation and R&D investment, with a strong emphasis on customizable, energy-efficient systems. Partnerships between equipment suppliers and plantation operators are expected to increase, aiming to optimize extraction efficiency and ensure compliance with evolving international quality standards. Overall, the sector’s outlook is robust, underpinned by evergreen demand for sandalwood oil and a global push toward sustainable, high-performance distillation technologies.
Key Players and Competitive Landscape
The competitive landscape of sandalwood distillation apparatus manufacturing in 2025 is shaped by a blend of traditional equipment producers and technologically progressive firms. This sector, vital for the extraction of high-value sandalwood oil, is seeing both consolidation and diversification as global demand for natural fragrances and therapeutic oils continues to rise.
Leading the market are specialized manufacturers in India and Australia—two of the world’s foremost sandalwood cultivation regions. Indian companies such as www.surabhiengineering.com and www.shrijiextraction.com have established significant footprints by offering a range of distillation units, including traditional batch-type and modern continuous systems. These firms emphasize corrosion-resistant materials and automation features, catering to both cottage industries and large-scale processors.
In Australia, with its robust plantation sandalwood industry, companies like www.quintis.com.au not only cultivate sandalwood but also invest in proprietary distillation facilities and collaborate with apparatus manufacturers for efficient, scalable extraction solutions. Their vertically integrated model allows for rapid adoption of new distillation technologies and quality improvements, setting industry benchmarks.
Elsewhere, European and Chinese manufacturers are entering the market with advanced stainless steel and glass distillation systems. Firms such as www.gmdu.net provide modular, export-oriented equipment, appealing to artisanal producers and exporters seeking compliance with international standards.
Recent years have also seen a trend towards energy-efficient and eco-friendly apparatus, reflecting both regulatory and buyer preferences. Manufacturers like www.surabhiengineering.com have begun to integrate heat recovery systems and digital process controls, minimizing energy consumption and maximizing oil yield. Customization has become a key competitive factor, with suppliers offering apparatus tailored to different sandalwood species, batch sizes, and extraction methods (hydrodistillation, steam distillation, etc.).
The outlook for the next few years suggests ongoing innovation and increased competition. As new regions, such as Southeast Asia and Africa, begin cultivating sandalwood, local apparatus manufacturers are expected to emerge, further diversifying the supplier base. Additionally, strategic partnerships between cultivators and equipment makers—exemplified by Australian industry models—are likely to proliferate, accelerating the adoption of next-generation distillation technologies.
Raw Materials Sourcing and Regulatory Compliance
Raw materials sourcing and regulatory compliance are critical factors shaping the sandalwood distillation apparatus manufacturing sector in 2025. The central raw materials include high-grade stainless steel, copper, specialized glass, and precision control components, all of which must meet stringent quality standards to ensure safety and product efficacy in essential oil extraction. As global demand for sandalwood oil remains robust, apparatus manufacturers are increasingly focused on securing reliable, ethically sourced materials while adhering to evolving regulatory landscapes.
The procurement of metals such as stainless steel and copper is influenced by volatile global supply chains. Leading manufacturers like www.borosil.com and www.sks-science.com emphasize sourcing certified, food-grade metals and laboratory glassware to ensure apparatus durability and compliance with international safety standards. In 2025, sustainability concerns are encouraging manufacturers to seek suppliers with responsible mining and recycling practices, responding to both regulatory and consumer pressures for greener production.
Compliance with international and regional regulations remains a top priority. In India—one of the world’s leading sandalwood processing hubs—manufacturers must ensure apparatus meets requirements laid out by authorities such as the Bureau of Indian Standards (BIS) and the Ministry of Environment, Forest and Climate Change (moef.gov.in). For example, apparatus that comes into contact with natural sandalwood oil must comply with IS 4450 and IS 1997 standards, which address material safety and equipment construction for essential oil distillation (www.bis.gov.in). In export markets, apparatus may also need CE marking or conformity with the European Machinery Directive, as referenced by manufacturers like www.gmpindia.net.
Another regulatory trend in 2025 is traceability and documentation. Authorities require apparatus vendors to maintain detailed records of material provenance and batch manufacturing, both to ensure product safety and to support sustainable sandalwood sourcing. Global initiatives such as the Convention on International Trade in Endangered Species of Wild Fauna and Flora (cites.org) also affect apparatus manufacturing indirectly, as they regulate the movement of sandalwood and related products, increasing scrutiny on equipment used in extraction processes.
Looking ahead, raw materials sourcing for sandalwood distillation apparatus is expected to become more transparent and regulated, with digital traceability solutions and greater emphasis on eco-friendly sourcing. Manufacturers will need to adapt to growing compliance requirements, particularly as the industry moves toward harmonized global standards and environmentally responsible production practices.
Advancements in Distillation Technologies and Automation
The landscape of sandalwood distillation apparatus manufacturing is rapidly evolving in 2025, driven by technological advancements and the growing demand for sustainable, high-purity essential oils. Traditionally, sandalwood oil extraction depended on steam distillation using copper or stainless-steel vessels. However, the sector is now witnessing an accelerated shift towards more energy-efficient, automated, and precision-controlled equipment.
One notable trend is the integration of automation and digital process monitoring. Modern apparatuses now feature programmable logic controllers (PLCs), real-time data acquisition, and remote monitoring capabilities, allowing operators to optimize temperature, pressure, and distillation time for maximum yield and quality. For example, www.keralastatecoir.com has begun incorporating IoT-enabled controls into their distillation units, enabling predictive maintenance and reducing downtime.
Manufacturers are also focusing on developing modular and scalable systems tailored for both large-scale industrial units and artisanal producers. Companies like www.essencetech.in and www.pilotsmithindia.com offer customizable distillation setups with advanced heat recovery mechanisms, which can reduce energy consumption by up to 30% compared to conventional systems. These innovations not only lower operational costs but also contribute to environmental sustainability—a growing concern among both producers and consumers.
Another significant advancement is the adoption of hybrid extraction techniques. Some apparatus manufacturers are now designing systems that combine steam distillation with supercritical CO2 extraction modules. This hybrid approach can enhance oil yield and purity, particularly for high-value sandalwood species. www.geainternational.com has reported ongoing R&D on adaptable platforms that facilitate both traditional and modern extraction techniques within a single integrated unit.
The outlook for sandalwood distillation apparatus manufacturing over the next few years is promising. With India and Australia leading global sandalwood cultivation, local equipment manufacturers are expected to expand exports, especially to Southeast Asia and Africa. Furthermore, stricter international quality standards are prompting apparatus producers to incorporate advanced filtration and fractionation modules, ensuring compliance and traceability. In summary, the sector is set to experience sustained growth, supported by digitalization, energy efficiency, and a focus on sustainable production methods.
Sustainability: Eco-friendly Manufacturing and Waste Management
The sandalwood distillation apparatus manufacturing sector is increasingly prioritizing sustainability, driven by both regulatory pressures and market demand for eco-friendly solutions. In 2025, manufacturers are emphasizing materials selection, energy efficiency, and responsible waste management as central to their operations.
A significant development is the shift from traditional metals to stainless steel and food-grade alloys, which offer both durability and recyclability. Companies like www.avagroind.com and www.essencestech.com highlight the use of stainless steel in their apparatus, citing its corrosion resistance, ease of cleaning, and long service life, which collectively reduce environmental impact by lowering maintenance and replacement rates.
Energy efficiency is another focus area, with leading apparatus manufacturers integrating improved insulation, optimized steam generation systems, and process automation to minimize fuel and water consumption. For example, www.avagroind.com showcases units that allow precise temperature control, reducing energy waste while maximizing oil yield. Such advances are aligned with global trends toward decarbonizing industrial processes and minimizing the carbon footprint of essential oil production.
Waste management within the apparatus manufacturing process and during distillation plant operation is gaining attention. Manufacturers are adopting closed-loop water systems and encouraging the use of biomass boilers, which utilize distillation byproducts as fuel, further reducing waste and reliance on external energy sources. Additionally, distillation residue management is being addressed, with manufacturers designing apparatus that facilitate the safe collection and composting of spent sandalwood chips, turning a former waste product into a resource. www.essencestech.com notes that modern plant designs incorporate residue handling systems to support this circular approach.
Looking ahead, the outlook for eco-friendly sandalwood distillation apparatus manufacturing is positive. Regulatory trends in India and Australia—the largest sandalwood producers—are expected to further incentivize greener manufacturing and operational practices. The adoption of ISO 14001 environmental management standards is becoming more common among equipment manufacturers, and there is growing collaboration with end-users to develop modular, scalable systems that reduce material waste and adapt to varying production volumes.
In summary, as the sandalwood oil industry seeks to balance profitability with environmental stewardship, apparatus manufacturers are responding with innovations in materials, energy use, and waste management. These changes are set to become industry norms over the next few years, ensuring that sandalwood distillation remains viable and responsible into the future.
Supply Chain and Distribution Channels
The supply chain and distribution channels for sandalwood distillation apparatus manufacturing are continuing to evolve in 2025, reflecting changes in global demand, regional production capacities, and advances in manufacturing technology. The supply chain begins with the procurement of specialized materials and components, such as stainless steel, high-grade copper, and advanced control systems, primarily sourced from industrial suppliers with established track records in equipment manufacturing. Companies like www.rosarioequipments.com in India and www.extractionmachinery.com are key manufacturers, sourcing raw materials both locally and internationally to ensure quality and compliance with export standards.
Manufacturers assemble components in dedicated workshops, increasingly adopting modular designs for easier customization and transport. These apparatuses, which range from small-scale units for cottage industries to large, fully automated plants for commercial distillers, are distributed through a mix of direct sales, regional representatives, and specialized industrial equipment dealers. For instance, www.gmpindia.net and www.gomatihydroherbals.com both utilize networks of agents and distributors to reach customers across Asia, Africa, and the Middle East, reflecting the international nature of demand for sandalwood oil extraction machinery.
In 2025, the distribution landscape is being shaped by increased digitalization. Many manufacturers now offer detailed product catalogs, remote consultation, and after-sales service coordination online, accelerating procurement times and improving transparency. This is particularly relevant as buyers in Australia, Southeast Asia, and Africa expand their sandalwood cultivation and oil production capacities, thus requiring timely access to distillation technology. Companies such as www.shriengineeringenterprises.com are investing in digital platforms to streamline order processing and provide technical support remotely.
Another emerging trend is the focus on end-to-end logistics solutions. Manufacturers increasingly coordinate with logistics partners to handle export documentation, packaging, and shipping to overseas clients, mitigating delays and ensuring compliance with international regulations on machinery and plant movement. Customization for regional requirements—such as voltage specifications or safety certifications—has become standard, further integrating supply chain flexibility with product design.
Looking forward, the next few years are expected to bring greater integration between manufacturers, suppliers, and end-users, enabled by digital supply chain management tools and stronger after-sales service networks. As sustainable sandalwood cultivation expands and distillation technology advances, manufacturers positioned with agile, robust supply chains and multi-channel distribution capabilities will be best placed to serve the growing and diversifying global market.
Regional Analysis: Production Hotspots and Emerging Markets
The manufacturing of sandalwood distillation apparatus is closely linked to regions with established sandalwood cultivation and a history of essential oil extraction. As of 2025, South Asia, particularly India, remains the principal production hotspot. Karnataka and Tamil Nadu, with their proximity to major sandalwood plantations and traditional distillation expertise, house several apparatus manufacturers and custom fabricators. Companies such as www.skpengineering.in and www.sreeabiramiengineeringworks.com continue to supply stainless steel, copper, and glass distillation units tailored for sandalwood oil extraction. Their facilities are often located close to sandalwood processing hubs, minimizing logistics costs and enabling close collaboration with oil producers.
In addition to India, Australia has emerged as a significant player both in sandalwood cultivation and in supporting apparatus manufacturing. The expansion of Indian and Australian sandalwood (Santalum album and Santalum spicatum) plantations in Western Australia has spurred local demand for distillation solutions. Firms such as www.sandalwood-australia.com and regional engineering workshops have begun customizing equipment for the unique processing needs of Australian-grown sandalwood, focusing on energy efficiency and sustainability.
China is also a rapidly growing market, both as an end-user of sandalwood oil and as a manufacturer of scalable distillation equipment. Chinese firms are leveraging advances in automation and stainless steel fabrication to produce modular apparatus for domestic use and export, supporting small and medium-sized essential oil enterprises throughout Asia. Manufacturers such as www.alibaba.com market a range of distillation units, from small-scale batch systems to industrial continuous distillers, reflecting the diverse needs of the sandalwood oil sector.
Other emerging markets include Southeast Asia (notably Indonesia and Vietnam) and East Africa (notably Kenya and Tanzania), where nascent sandalwood replanting programs are creating demand for distillation infrastructure. While local manufacturing capacity in these regions is still developing, there is increasing collaboration with Indian and Chinese suppliers to establish regional assembly and servicing hubs.
Looking ahead, the outlook for sandalwood distillation apparatus manufacturing remains positive, driven by rising global demand for sandalwood oil in perfumery, cosmetics, and pharmaceuticals. Environmental and regulatory pressures are prompting apparatus makers to innovate toward higher efficiency and reduced emissions. The next few years are expected to see further decentralization of production, with more regional workshops and technology transfers to meet the needs of emerging sandalwood-producing countries.
Customer Segments and End-User Applications
The customer segments and end-user applications for sandalwood distillation apparatus manufacturing are evolving rapidly in 2025, shaped by shifting market demand, regulatory changes, and technological innovation. Traditionally, the primary customers have been essential oil producers, especially those specializing in high-value natural fragrances and aromatherapy products. However, the scope is broadening to include pharmaceutical companies, research institutions, and even luxury cosmetics brands seeking control over proprietary extraction processes.
In India and Australia—two leading regions for sandalwood cultivation—manufacturers such as www.ambicamachinery.com and www.geainternational.com provide custom and standardized distillation units to a diverse clientele. Essential oil producers remain the largest segment, with demand driven by the global popularity of sandalwood oil in perfumery, personal care, and wellness products. For example, Indian firms like www.sandalwoodoil.com invest in advanced apparatus for both batch and continuous distillation processes to meet purity and sustainability standards.
Pharmaceutical and biotechnology companies are emerging as a significant customer group, leveraging sandalwood extracts for their antimicrobial and anti-inflammatory properties. These end-users often require apparatus that complies with GMP standards and offers precise control over extraction parameters. In 2025, manufacturers have responded by developing skid-mounted, modular distillation systems tailored to research and pilot-scale production, as seen in the product offerings from www.stilldragon.com.au.
Another growing segment comprises academic institutions and government research bodies. With increased research into sustainable harvesting, alternative feedstocks, and novel extraction methods, universities and R&D centers are procuring specialized distillation equipment for pilot studies. For instance, collaborative projects between industry and academia in Australia and India are fueling demand for apparatus with advanced monitoring and automation features (www.ambicamachinery.com).
Looking ahead, the outlook for customer diversification is strong. The luxury cosmetics and personal care industry is expected to invest further in in-house distillation to assure traceability and quality. Meanwhile, regulatory emphasis on sustainable sourcing and traceable production will push apparatus manufacturers to integrate smart monitoring, IoT, and energy-efficient features into their designs. Expansion into global markets—particularly Southeast Asia and Africa, where sandalwood cultivation is expanding—will also broaden the customer base for distillation apparatus manufacturers in the coming years (www.geainternational.com).
Future Outlook: Challenges, Opportunities, and Strategic Recommendations
The sandalwood distillation apparatus manufacturing sector is poised for significant transformation in 2025 and beyond, driven by evolving market demand, regulatory shifts, and technological innovation. However, the industry faces a complex landscape of challenges and opportunities that will shape its trajectory over the next few years.
Challenges:
- Raw Material Sourcing: The sustainability and availability of sandalwood—especially Santalum album—remain critical concerns. Manufacturers of distillation apparatus will need to adapt their designs for use with alternative or cultivated sandalwood sources, as wild supplies remain under regulatory scrutiny and CITES protection (www.cites.org).
- Regulatory Compliance: Increasing environmental oversight affects both the distillation process and apparatus design. Compliance with emissions, energy efficiency, and waste management norms is becoming stricter, particularly in major manufacturing hubs like India and Australia (www.karnataka.gov.in).
- Technological Barriers: Traditional stills are being replaced with advanced, automated systems that demand higher capital and specialized expertise for manufacturing. Small and mid-sized apparatus fabricators may struggle to keep pace with these technological shifts (www.goma.co.in).
Opportunities:
- Process Innovation: The adoption of continuous distillation systems, improved heat recovery, and precision controls offers apparatus manufacturers the chance to deliver greater yield and energy savings for clients. Companies such as www.goma.co.in and www.essencenindia.com are already offering modernized, scalable equipment to global buyers.
- Global Market Expansion: With growing demand for natural essential oils in perfumery, cosmetics, and wellness, apparatus manufacturers can target new geographies, especially Southeast Asia and Africa, where sandalwood plantations are increasing (www.tfs.com.au).
- Customization and After-sales Services: Offering modular designs, remote monitoring, and comprehensive maintenance packages can differentiate manufacturers and build long-term client relationships.
Strategic Recommendations:
- Invest in R&D for more efficient, eco-friendly apparatus suited to cultivated sandalwood and alternative species.
- Forge partnerships with plantation operators and essential oil producers to co-develop tailored solutions and ensure apparatus compatibility with evolving feedstock quality (www.quintis.com.au).
- Develop training and support programs to help clients transition from traditional to automated systems, enhancing brand loyalty and market reach.
In summary, while the sandalwood distillation apparatus manufacturing sector faces regulatory and technological headwinds, the coming years offer robust prospects for those able to innovate and strategically align with the evolving global value chain.